A point of pride for the SōRSE team is our relationship with our clients and our willingness to help in whatever way we can to get their product to market – from recommending flavor profiles to connecting them with co-manufacturers.
Nearly a year ago, one of our clients, Cann, a low dose social tonic, was looking to expand to other legal markets beyond California where they are based, but they did not have a way to produce SōRSE emulsion, the backbone of their beverage. Zach Hershberger, our Operations Manager, and the Operations team put their heads together and came up with a plan – create a mobile unit and take production on the road.
Recently we sat down with Zach, who has executed many of the mobile production runs, to talk about how this service came to be, what they entail, the benefits this provides to a client like Cann, and the service might expand in the future.
What is the genesis story of the first mobile run?
The whole process was born out of a request from Cann, who wanted to expand to Nevada. They basically said that “There was no Cann without SōRSE,” that SōRSE was an integral part of their product. That led to them asking if we could produce SōRSE with their license holder in Nevada. At first we thought it was going to be pretty tough to install a lab in a new location, but then we realized it was feasible to take our equipment on the road and set up shop at the license’s facility. That first trip to Nevada was May of 2020.
How did SōRSE’s and your relationship with Luke Anderson and Jake Bullock from Cann develop over time?
I had just started at SōRSE when the company was ramping up emulsion production when Luke and Jake, Cann’s Co-Founders, visited the office in Seattle as they were evaluating emulsion suppliers. At that point, they were planning on operating out of San Diego. I shared some of my experience working at GreenMed Labs where we produced Happy Apple, just to give them an idea of what beverage production entailed. At that point, they knew what their product was going to be; they just weren’t sure where and how they were going to make it. I think one reason they went with us is that they realized we understood what they needed to accomplish.
After they signed on with us as a client, I made sure they were taken care of, oversaw the production of their emulsion in California, and coached them through the processes that they needed to get production off the ground. Eventually they hired Ishan Kapoor, their Director of Operations, and I have been working with him since.
What did you think of the idea behind Cann’s product, a low dose social tonic?
I like the idea of a low dose beverage – I think it’s a great entry point for someone who is curious about infused beverages. It seemed like they had good idea behind it – a beverage to replace an alcoholic drink – and I really appreciated their commitment to using high quality ingredients. They refuse to compromise on the quality, and it shows in their product. It really seemed like a craft beverage.
What does the timeline look like for planning and executing a mobile run?
The calendar and the planning really depend on where we are going. If we are going across the country, it takes time to ship the equipment to the location. If we are driving, you have to factor in the travel time. We recently introduced a second crate of equipment to the mix, so that should make things a little easier.
The timeline works like this: A customer contacts us and asks us when we can make it; then our team looks at the calendar to establish a date. Once confirmed, we get the run on the calendar and start getting the ball in motion for what we need to do to execute it. That includes sending a packet of information to the client, basically their to-do list, and in turn they need to send us a Certificate of Analysis (COA) of the cannabis raw material they are using. The goal is that two weeks beforehand, we have all the details buttoned up. Facility requirements need to be met so that it is ready to go when we get there.
Once we get to the facility, we take stock of the material and equipment we shipped and make sure we have everything we need. Then we set up the equipment for production. On Day 2, we start the conversion of the oil to the emulsion, starting the conversion. Converting a kilo typically takes two days using our mobile lab’s equipment. Day 3 is our wrap up, clean up, and package the equipment to be shipped back. I feel good about how efficient we are on these runs; the key to a successful run is maximizing our time so that we are not wasting our resources.
In what states have you done mobile runs since this service started?
We’ve gone to California, Nevada, Rhode Island, Massachusetts, and Illinois.
What do you enjoy about mobile runs? What’s challenging about them?
What’s cool is seeing the interest and curiosity of the people working at the license facility in what we are doing and why. Basically when this big crate arrives, they are wondering what’s in it, and then once we arrive and set it up, they are wondering what we’re doing with it. This process is very different from the other processes going on at the facility, and they are inherently curious about what companies do with the emulsion. We find ourselves explaining what we are doing, who we are doing it for, and why. This exposes them to a world beyond flower – something so different from what they are used to.
The challenges are adapting to the different facilities, assessing the spaces where we are working, and being able to respond to situations and snags quickly. At this point we are used to it – and we have learned how to adapt to new environments and problem-solve quickly.
Why do you think it is important that SōRSE offer this service, and how does it benefit a partner like Cann? How does it benefit SōRSE?
I think that offering this level of service to our clients shows that we see ourselves as partners in their expansion and overall success. It also gives our clients consistency in their product because we are using the same equipment and ingredients we do at our own facility. I think they know that not every supplier will have the capability to do a run in a new state like we do. Mobile runs have been beneficial for us, because we have been able introduced to partners and potential partners in new states. We have also learned a lot about how licenses work, and how differently they operate.
A year from now, what will mobile runs look like for SōRSE?
If things continue to progress the way they have been, I think we will have more employees on the road doing these conversions. I see us doing higher volumes through trusted locations instead of small volumes in many locations – maybe two to three conversions a month. We will look to find trusted partners in each state where we can work consistently. Those partners can then act as a reseller to other companies who are interested in SōRSE. I would love to see us get to a point where the license was wholesaling SōRSE to other companies for make their own products.
Let’s Chat
Want to evaluate our emulsions? We’d love to learn more about your business and work to create a custom solution.
Tell us a little about yourself and we’ll be in touch shortly.
Privacy Policy. All rights reserved 2021.
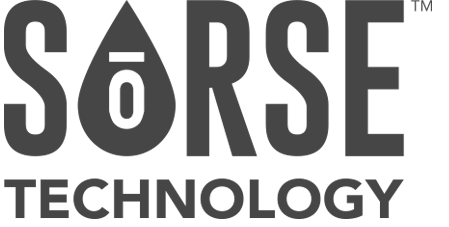
Let’s Chat
Want to evaluate our emulsions? We’d love to learn more about your business and work to create a custom solution.
Tell us a little about yourself and we’ll be in touch shortly.
Privacy Policy. All rights reserved 2021.
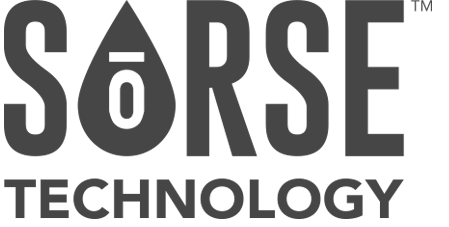
Let’s Chat
Want to evaluate our emulsions? We’d love to learn more about your business and work to create a custom solution.
Tell us a little about yourself and we’ll be in touch shortly.
Privacy Policy. All rights reserved 2021.
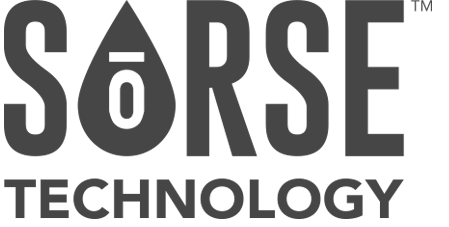
A
better
emulsion
Here is our step-by-step guide on water-soluble emulsion technology’s impact on stability.